Multi-Step Job Workflow Optimization
Managing multiple print jobs—especially those with complex, multi-stage production requirements—can be a logistical headache. Lost details, misordered steps, and communication breakdowns quickly lead to delays and increased costs. If you've ever scrambled to track down job specs or juggled overlapping deadlines, you're not alone. The key to overcoming these challenges is a systematic approach that brings clarity to every workflow stage. This guide is your blueprint for transforming chaos into order: you'll learn how to gather critical job info, map precise production sequences, allocate staff and machines wisely, and continuously improve your process. Say goodbye to fire drills and bottlenecks—start routing print jobs with confidence and control.
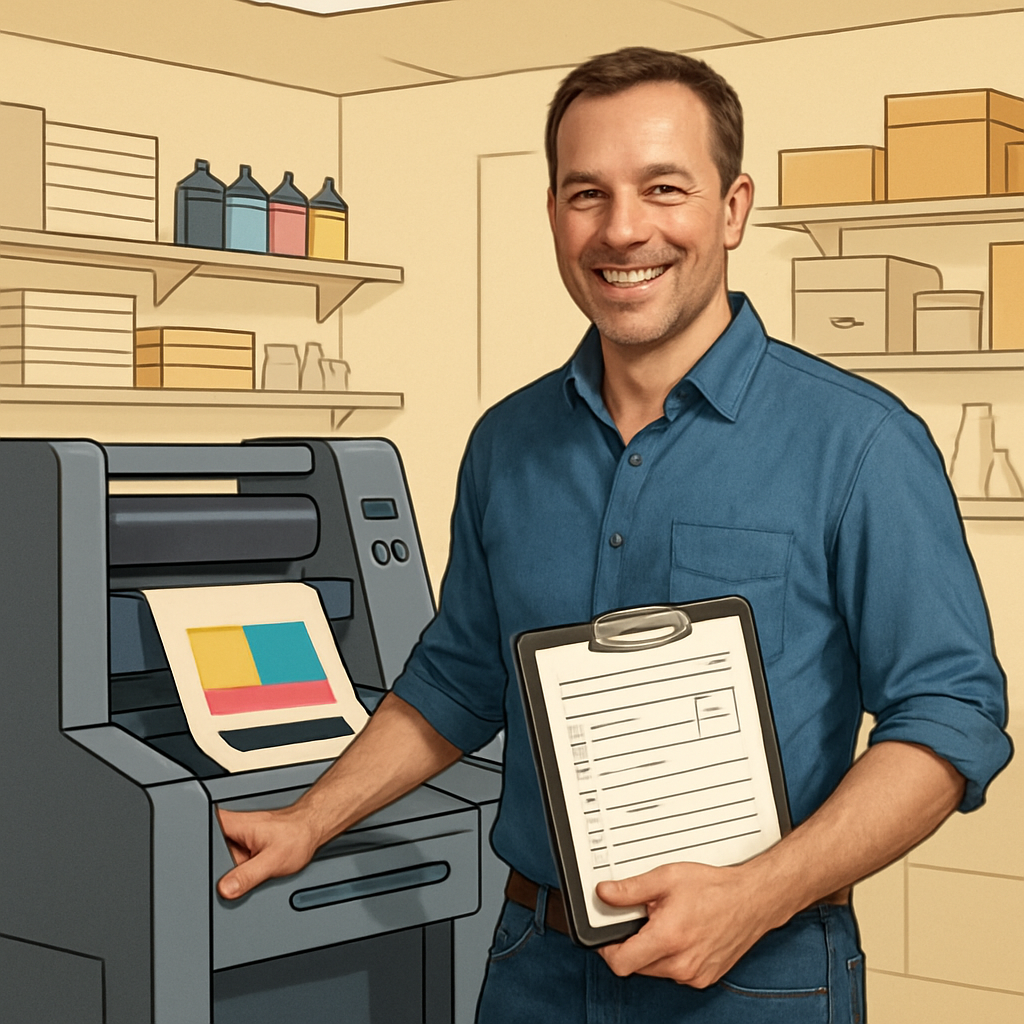
Important Considerations
Ensure success and avoid pitfalls by keeping these important notes in mind throughout the workflow routing process:
- Handle client data and instructions with care—errors can lead to costly reprints
- Be aware of regulatory and safety compliance for sensitive or complex jobs
- Anticipate machine maintenance or downtime and include contingencies in schedules
- Protect sensitive client information; follow confidentiality protocols as needed
- Double-check job specs before assigning steps to avoid miscommunication
- Document adjustments and exceptions for future reference and process improvements
Minutes Saved
Every Time Used
Minutes To Set Up
Workflow Guide For
Multi-Step Job Workflow Optimization
Setting Up for Success
Start with the right preparation to ensure your print job workflow runs smoothly. Gather all necessary information, resources, and access before diving in:
- Access to order entry/job management systems
- Updated list of all current and upcoming print jobs
- Full job specifications—including client notes and special instructions
- Production process documentation (step requirements, typical durations)
- Knowledge of available machines and operator skillsets
- Open communication channels with sales, production, and finishing teams
Important Considerations
Ensure success and avoid pitfalls by keeping these important notes in mind throughout the workflow routing process:
- Handle client data and instructions with care—errors can lead to costly reprints
- Be aware of regulatory and safety compliance for sensitive or complex jobs
- Anticipate machine maintenance or downtime and include contingencies in schedules
- Protect sensitive client information; follow confidentiality protocols as needed
- Double-check job specs before assigning steps to avoid miscommunication
- Document adjustments and exceptions for future reference and process improvements
Follow these steps to streamline your workflow and enhance operational efficiency in your role.
Start Here
Step 1: Gather Job Details and Requirements
"List all print jobs currently in the queue that require multiple production steps (e.g., print, cut, bind). For each job, provide the specific requirements, due dates, and any special instructions."
Goal
To collect and organize all relevant information for jobs needing multiple production processes in order to create an efficient workflow plan.
Example
"List all jobs that need printing, cutting, and binding this week, including their deadlines and any client-specific requirements."
Variations
- "What are all active jobs that require more than one step in production?"
- "Show me print jobs due this week with multiple finishing processes."
Troubleshooting
- Missing or incomplete job data: Double-check order entry systems or request missing details from the sales team or order intake desk.
- Unclear requirements: Clarify with customers or job originators to ensure accuracy before proceeding.
Step 2
Step 2: Map Out Production Steps and Sequences
"For each multi-step job, break down the required production stages in correct order (e.g., print first, then cut, then bind) and identify any dependencies or minimum wait times between steps."
Goal
To ensure that each job's workflow is clearly defined, minimizing confusion and production delays due to misordered tasks or unrecognized dependencies.
Example
"For Job #1023, the sequence is: 1) Digital Print, 2) Laminate (must cure for 1 hour), 3) Contour Cut, 4) Bind. List any steps that cannot overlap."
Variations
- "Show step-by-step workflow for jobs with print, cut, and bind, including timing requirements between steps."
- "Identify jobs where steps can be done in parallel versus sequentially."
- "Flag any jobs that need extra drying/curing time before finishing."
Troubleshooting
- Conflicting step orders: Reassess the sequence and consult production leads to resolve any bottlenecks or process overlaps.
- Unknown process dependencies: Refer to machine specs or ask process experts for typical wait/cooldown times when unsure.
Step 3
Step 3: Allocate Resources and Schedule Workflow
"Assign each job step to available machines and operators based on their capacity and expertise. Create a proposed production schedule that maximizes machine usage and meets all job deadlines."
Goal
To optimize the use of machines and staff so that all jobs progress efficiently through each production stage and delivery timelines are achieved.
Example
"Assign Job #1023's print stage to Printer A at 9:00 AM, then transfer to Cutting Table B at 11:00 AM, with Binding Team starting at 2:00 PM. Ensure no step conflicts with other priority jobs."
Variations
- "Build a production schedule for all multi-step jobs this week, aiming for minimal machine downtime."
- "Prioritize jobs with the earliest due dates in resource allocation."
Troubleshooting
- Machine or operator not available: Adjust the schedule, considering alternate machines or overtime if urgent.
- Bottlenecks identified: Shift lower-priority jobs or redistribute resources to clear critical paths.
Step 4
Step 4: Monitor Job Progress and Handle Exceptions
"Track the real-time status of each job and flag any delays, machine issues, or resource shortages. Propose adjustments to keep workflows on track and communicate changes to the team."
Goal
To maintain workflow efficiency by staying aware of progress, quickly addressing disruptions, and minimizing impact on downstream steps and deadlines.
Example
"Job #1023 has a delay at the cutting stage due to machine maintenance. Update the schedule and reassign the binding step if needed, notifying the bindery team and sales rep immediately."
Variations
- "Notify me if any job is at risk of missing its deadline due to workflow holdups."
- "Suggest contingency plans if a key machine goes offline."
- "Automatically update the team on any rescheduling that affects handoffs."
Troubleshooting
- Unreported delays: Set up systematic check-ins or real-time dashboards to flag slowdowns promptly.
- Poor team communication: Use automated alerts or shared job boards to keep everyone aligned on status changes.
Step 5
Step 5: Review and Refine Workflow Processes
"After completing a set of jobs, analyze the workflow data to identify bottlenecks, inefficiencies, or frequent error points. Recommend process improvements or automation opportunities for future jobs."
Goal
To continually improve workflow routing, reducing waste and errors while increasing capacity and turnaround speed for future production cycles.
Example
"Analyzing last month’s jobs shows frequent holdups at the binding stage after 4 PM. Recommend schedule adjustments or cross-training to address this consistent bottleneck."
Variations
- "Provide a summary of workflow bottlenecks for jobs over the past month."
- "Highlight which production steps frequently required rework or correction."
- "Suggest where investing in new equipment could yield a significant efficiency gain."
Troubleshooting
- Inadequate data for analysis: Ensure all production steps are logged accurately and consistently. Consider implementing barcode scanning or job tracking software.
- No clear improvement opportunities: Solicit feedback from floor staff or review industry best practices for optimization ideas.
Step 6
Step 7
What You'll Achieve
By following this guide, your multi-step print jobs will flow efficiently from intake to delivery. You'll eliminate guesswork in job planning, reduce last-minute scrambles, and deliver on-time, high-quality results that satisfy both clients and your team. Each job will move seamlessly through the correct production stages, with full visibility into timelines and resource use. Ultimately, you'll gain confidence in your workflow's reliability and be able to consistently deliver projects without costly errors or delays.
Measuring Your Success
Success in workflow routing for multi-step print jobs is measured by timeliness, resource usage, and lowered error rates. These metrics can help you track improvements:
- Job completion rate on or before due date
- Reduction in production bottlenecks
- Decrease in rework or error corrections
- Machine and operator utilization efficiency
- Number of jobs delivered without rescheduling
- Feedback from team on process clarity
Troubleshooting Your Workflow
Navigating workflow challenges can be daunting. This guide offers practical troubleshooting tips and innovative strategies to enhance your AI implementation.
Pro Tips & Tricks
- Create reusable workflow templates for similar multi-step job types
- Use color-coded job boards or dashboards for instant status visibility
- Schedule buffer times between steps to absorb minor delays without impacting deadlines
- Regularly cross-train staff for key steps to prevent bottlenecks
- Leverage automated notifications for hands-offs between production stages
- Track actual step times versus estimates for ongoing accuracy improvements
- Set up recurring workflow review meetings for continuous learning
Common Issues & Solutions
Even well-planned workflows can hit snags. Here are some frequent problems and how to solve them:
- Issue: Missing job details at intake
Solution: Implement mandatory fields or intake checklists before jobs begin. - Issue: Overlapping production steps causing bottlenecks
Solution: Review dependencies and allocate buffer times to prevent overlap. - Issue: Machine breakdown or operator absence
Solution: Prepare alternative schedules and cross-trained backups for key steps. - Issue: Communication failures between teams
Solution: Use shared dashboards, alerts, and regular check-ins to keep everyone aligned. - Issue: Incomplete step tracking
Solution: Adopt digital logging or barcode scanning for each workflow stage.
Best Practices to Follow
- Standardize data collection for every incoming job
- Confirm step sequences and dependencies during kickoff meetings
- Maintain transparent, real-time workflow tracking accessible to all stakeholders
- Prioritize jobs with tight deadlines in scheduling
- Log all job adjustments and exceptions for process review
- Follow all safety and compliance guidelines for equipment and data
- Encourage open feedback from production staff for continuous improvement
Ready to Optimize Your Print Workflow?
Stay ahead in print production by mastering more step-by-step guides like this. Sign up for our WorkflowGuide.com newsletter and get tips, checklists, and new process templates delivered to your inbox!
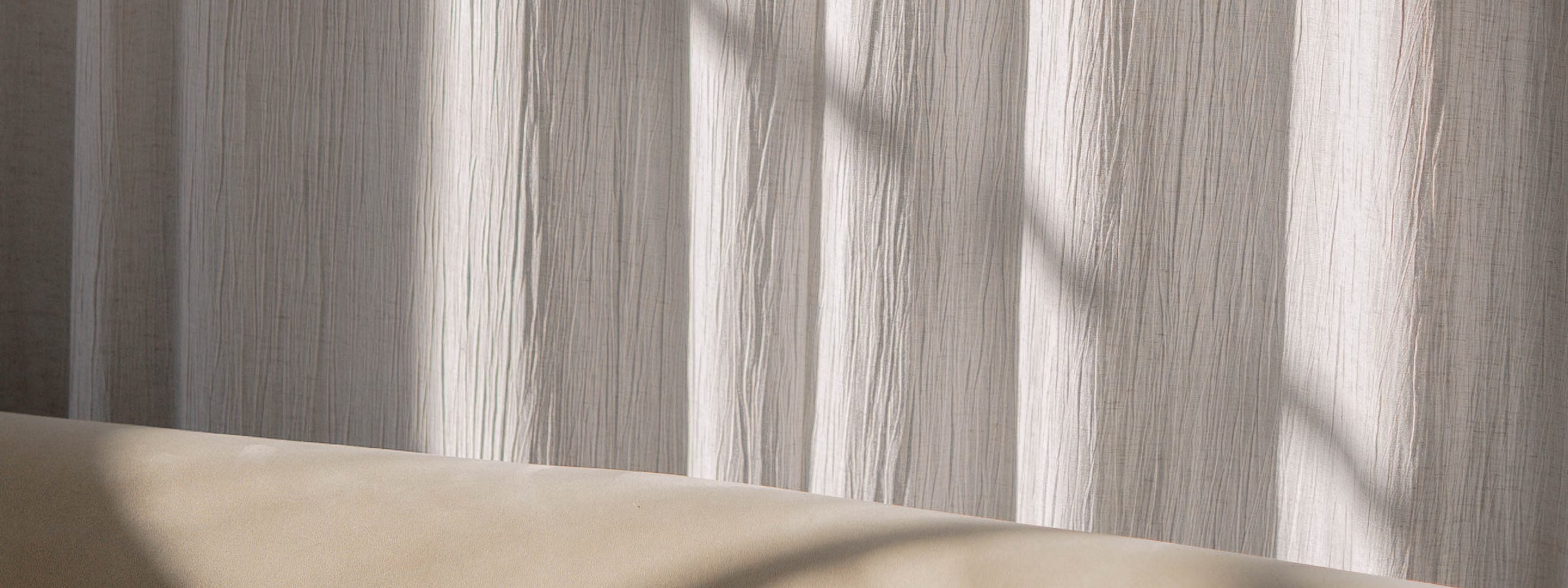
Streamline Your Daily Tasks
Discover AI solutions tailored for your role.
Multi-Modal Shipment Coordination Task
Simplify multi-modal shipments! Follow clear steps to organize, quote, and track carrier deliveries for seamless logistics. Save time now!
AI-Based Related Maintenance Suggestions
Streamline vehicle maintenance recommendations. Follow these clear steps to boost accuracy and customer trust while saving time.
Find Sheet Music & Exercises by Level & Goals
Discover how to efficiently find and assign tailored sheet music for your students. Streamline music selection with organized, actionable steps.
Stuck on a Tricky Implementation?
Let's Debug Together!
Book a 30-minute strategy session with our AI workflow wizards. We'll dive into your specific challenges, troubleshoot like pros, and map out optimization opportunities that'll make your workflows purr like a well-maintained server. No sales pitch, just solutions (and maybe a nerdy joke or two).
Explore More Guides to Enhance Your AI Implementation Journey
Discover Additional Resources Tailored for Your Industry Needs
These guides offer valuable insights and practical steps for effective AI integration.
Unlock the Potential of AI in Your Business Operations
Gain access to expert strategies and tools to streamline your processes.
Enhance Your Skills with Our Comprehensive AI Resource Guides
Find the right guide to elevate your understanding and application of AI.