Tech Scheduling Optimization by Skills & Bays
Auto repair shops often struggle with chaotic schedules, overbooked technicians, and underused bays. Juggling job priorities, technician skills, and limited resources often results in lost productivity, longer customer wait times, and unnecessary stress. Our actionable step-by-step guide tackles these frustrations head-on. By carefully gathering job details, matching technicians' skills to assignments, analyzing bay availability, and conducting a thorough review before communication, you'll transform the way work is scheduled. Achieve faster turnaround, happier staff, and optimal shop utilization—all with a process designed to eliminate confusion and idle time.
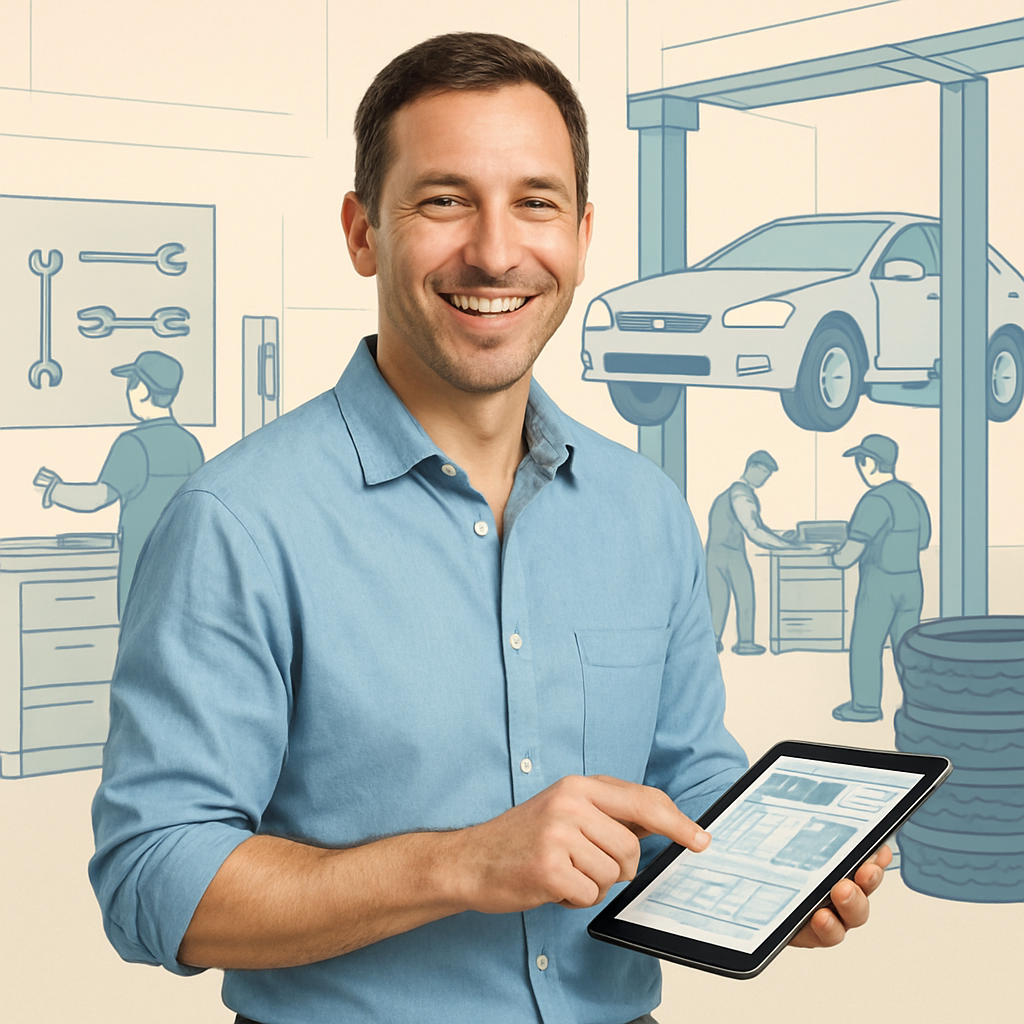
Important Considerations
Keep shop safety, accuracy, and regulatory compliance in mind throughout scheduling to avoid costly mistakes. Document any exceptions or changes for transparency.
- Protect sensitive employee and customer data at all times
- Follow safety protocols when assigning jobs to ensure technicians are certified for required tasks
- Record any scheduling changes for audit or reporting needs
- Check for updated shop policies that may impact shift scheduling or overtime
- Notify team in case of bay maintenance or emergency closures
Minutes Saved
Every Time Used
Minutes To Set Up
Workflow Guide For
Tech Scheduling Optimization by Skills & Bays
Setting Up for Success
Before starting, gather the information and tools required for seamless scheduling. Preparation streamlines the workflow and nips potential issues in the bud.
- Access to daily/weekly repair job list (work order management system)
- Technician roster with skill/certification details
- Up-to-date bay schedule (including maintenance status)
- Sufficient knowledge of shop tools/software used for scheduling
- Ability to communicate schedules to all involved parties (email, SMS, physical boards)
Important Considerations
Keep shop safety, accuracy, and regulatory compliance in mind throughout scheduling to avoid costly mistakes. Document any exceptions or changes for transparency.
- Protect sensitive employee and customer data at all times
- Follow safety protocols when assigning jobs to ensure technicians are certified for required tasks
- Record any scheduling changes for audit or reporting needs
- Check for updated shop policies that may impact shift scheduling or overtime
- Notify team in case of bay maintenance or emergency closures
Follow these steps to streamline your workflow and enhance operational efficiency in your role.
Start Here
Step 1: Gather and Organize Job Details
"List today's repair jobs along with their estimated duration, required skill level, and any special equipment or bay needs."
Goal
Compile a clear, detailed inventory of all repair jobs for the period, ensuring all necessary information is recorded for scheduling.
Example
"Today's jobs: 1) Brake pad replacement – 2 hours, intermediate, standard bay; 2) Transmission diagnostics – 3 hours, advanced, diagnostic bay; 3) Oil change – 1 hour, beginner, any bay."
Variations
- "Summarize tomorrow's scheduled repairs with skill requirements and estimated times."
- "Export a list of open work orders including job complexity and bay constraints."
Troubleshooting
- Missing Job Details: Review work order system or call customers for missing service details.
- Ambiguous Job Complexity: Consult repair manuals or technicians to estimate required skill level.
Step 2
Step 2: Assess Technician Skills and Availability
"Provide a roster of available technicians for today and list their certifications and known specialties."
Goal
Identify which technicians are available, their working hours, and the types of jobs they are qualified to do.
Example
"Available technicians: Alex – 8am-4pm, ASE Master, transmission specialist; Jamie – 9am-5pm, brakes/fluids certified; Mark – covering bodywork, 10am-6pm."
Variations
- "List all techs scheduled tomorrow, with skill ratings and current workload percentages."
- "Who is off or on vacation this week? Show skills matrix for on-duty staff."
Troubleshooting
- Unclear Skill Sets: Reference technician HR files or ask the shop foreman for updated certifications.
- Overlapping Time Off: Double-check scheduling software and recent vacation approvals.
Step 3
Step 3: Analyze Bay Availability and Constraints
"Show a timeline of bay usage for today, noting any bays under maintenance or reserved."
Goal
Ensure up-to-date awareness of which bays are available, any special features (e.g., lifts, diagnostic equipment), and downtime during the scheduling period.
Example
"4 bays: Bay 1 open all day (standard), Bay 2 8am-1pm (lift), Bay 3 closed for repair, Bay 4 open after noon (diagnostics)."
Variations
- "Which bays are available for heavy vehicles today and when?"
- "List any upcoming bay or lift maintenance that may interfere with scheduling this week."
Troubleshooting
- Conflicting Bay Usage: Cross-verify bay bookings in scheduling software and check with floor manager for unscheduled uses.
- Unnoted Maintenance: Confirm with shop maintenance logs and communicate with the building manager.
Step 4
Step 4: Generate and Review the Preliminary Schedule
"Create a draft schedule matching each job to a qualified technician and an available bay, aiming to minimize idle time and maximize throughput."
Goal
Produce an initial, optimized assignment of jobs to technicians and bays, considering skill match, job order, and time slots.
Example
"8am: Alex – Transmission diagnostics in Bay 4; Jamie – Brake pad replacement in Bay 2; Mark – Oil change in Bay 1 at 10am."
Variations
- "Show an alternate schedule prioritizing shortest jobs first."
- "Optimize schedule to fit all jobs before 5pm given projected durations and technician overlap."
Troubleshooting
- Schedule Conflicts: Adjust job start times or swap technician assignments to resolve double-bookings.
- Overlooked Jobs: Double-check the job list and confirm all active work orders are scheduled.
Step 5
Step 5: Validate Schedule Against Constraints and Communicate Assignments
"Review the draft schedule for conflicts, skill mismatches, or idle periods, then prepare the final assignment list to share with technicians."
Goal
Finalize the schedule, resolve any remaining issues, and ensure all stakeholders have clear instructions for the day.
Example
"After review: Confirmed Alex has no overlapping jobs, Jamie scheduled within working hours, all bays appropriately matched. Email schedule sent to technician team, update board in shop."
Variations
- "Highlight any technicians under-utilized and re-balance assignments."
- "Export finalized schedule to SMS, shop board, or management software."
Troubleshooting
- Technician Pushback: Be prepared to explain assignment rationales; solicit feedback for adjustments.
- Communication Delays: Double-check delivery of assignments and post backup copies in common areas.
Step 6
Step 7
What You'll Achieve
Upon completing these steps, the shop will have a robust, conflict-free schedule tailored to each technician’s skills and bay availability. This results in smooth operations, minimal idle time, and higher staff morale. Customers will benefit from quicker service, and managers will see increased throughput and fewer day-of disruptions. The entire team will enjoy the confidence that every job is matched to the right resource at the right time, driving satisfaction and repeat business.
Measuring Your Success
Track your scheduling improvements by measuring efficiency, technician utilization, and error rates. Expect shorter turnaround times, fewer conflicts, and increased job completion rates.
- Technician idle time reduced
- Bays utilized effectively
- Fewer schedule conflicts or overlaps
- On-time job completion rate increased
- Staff satisfaction scores regarding schedules
- Repeat work due to scheduling errors minimized
Troubleshooting Your Workflow
Navigating workflow challenges can be daunting. This guide offers practical troubleshooting tips and innovative strategies to enhance your AI implementation.
Pro Tips & Tricks
- Color-code schedules for quick visual reference (by bay, job priority, or technician skill)
- Keep a running notes section for vacation/absence forecasting
- Use automated reminders for schedule changes
- Build in buffer times for unexpected delays or walk-ins
- Leverage technician feedback to refine future schedules
- Regularly update skills/certification records in your system
- Save templates for common job groupings to speed up scheduling
- Validate schedule in multiple views (timeline, technician, bay) before finalizing
Common Issues & Solutions
Stay alert for these frequent shop scheduling hitches and use these tactics for fast resolution:
- Issue: Missing job information
Solution: Cross-check open work orders and call customers if needed. - Issue: Technician skill mismatch
Solution: Review certifications and swap assignments as needed. - Issue: Overlapping job times for a technician
Solution: Adjust job start times or redistribute workload. - Issue: Bay maintenance overlooked
Solution: Update schedules after checking maintenance logs. - Issue: Communication breakdowns
Solution: Use multiple channels (email, text, shop board) to confirm assignment delivery.
Best Practices to Follow
- Double-check job requirements against technician certifications
- Review bay assignments for special equipment needs
- Confirm all schedule communications are acknowledged
- Regularly audit past schedules for improvement opportunities
- Maintain clear documentation for all assignments and changes
- Adhere to staff workload balance to avoid burnout
- Stay informed about new compliance or safety regulations
Supercharge Your Shop's Scheduling!
Ready to boost efficiency, reduce stress, and keep your technicians and customers happy? Sign up for our newsletter to get more time-saving guides, workflow checklists, and exclusive auto shop management insights.
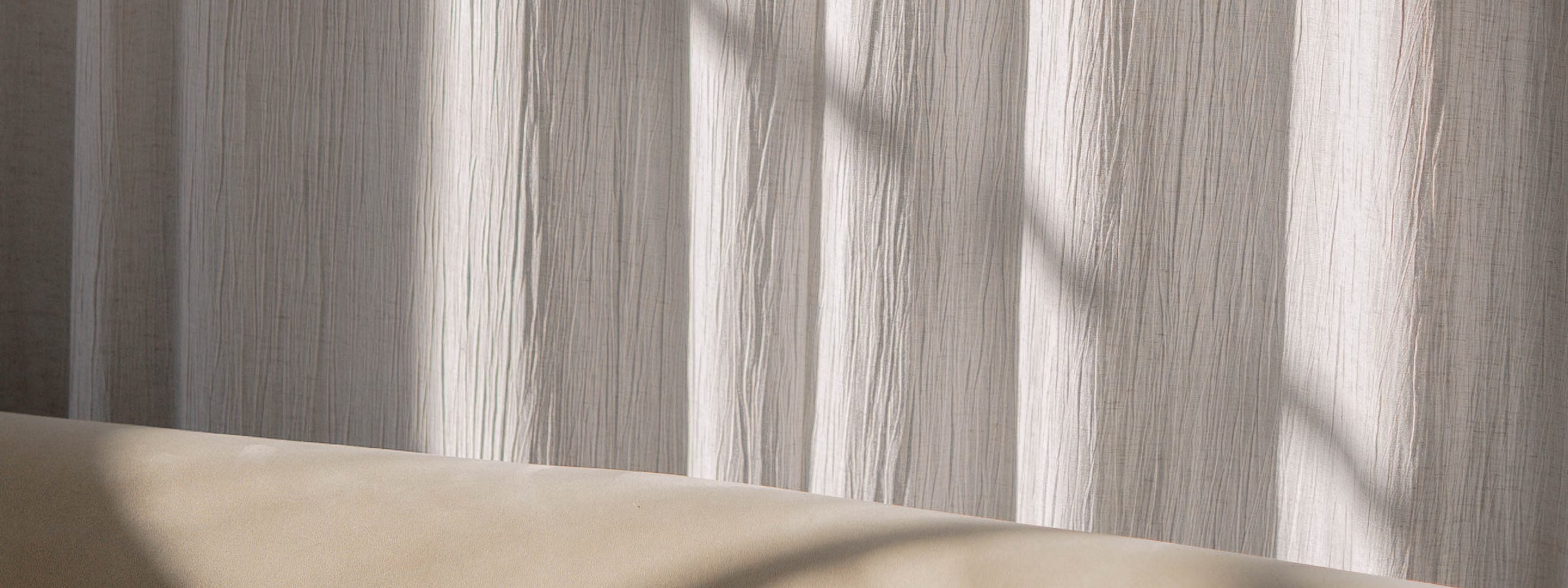
Streamline Your Daily Tasks
Discover AI solutions tailored for your role.
Multi-Modal Shipment Coordination Task
Simplify multi-modal shipments! Follow clear steps to organize, quote, and track carrier deliveries for seamless logistics. Save time now!
AI-Based Related Maintenance Suggestions
Streamline vehicle maintenance recommendations. Follow these clear steps to boost accuracy and customer trust while saving time.
Find Sheet Music & Exercises by Level & Goals
Discover how to efficiently find and assign tailored sheet music for your students. Streamline music selection with organized, actionable steps.
Stuck on a Tricky Implementation?
Let's Debug Together!
Book a 30-minute strategy session with our AI workflow wizards. We'll dive into your specific challenges, troubleshoot like pros, and map out optimization opportunities that'll make your workflows purr like a well-maintained server. No sales pitch, just solutions (and maybe a nerdy joke or two).
Explore More Guides to Enhance Your AI Implementation Journey
Discover Additional Resources Tailored for Your Industry Needs
These guides offer valuable insights and practical steps for effective AI integration.
Unlock the Potential of AI in Your Business Operations
Gain access to expert strategies and tools to streamline your processes.
Enhance Your Skills with Our Comprehensive AI Resource Guides
Find the right guide to elevate your understanding and application of AI.