Optimize Warehouse Order Picking Routes
Order picking is often the most time-consuming and error-prone task in warehouse management, leading to delayed shipments, mis-picks, and frustrated staff. If you’ve ever struggled with missing items, backtracked routes, or last-minute priority orders confusing your workflow, you’re not alone. This guide provides a clear, step-by-step process to help you streamline and organize your warehouse picking process. By following these proven strategies, you’ll reduce wasted time, avoid common mistakes, and ensure that every order is picked quickly and accurately—making you, your team, and your customers happier.
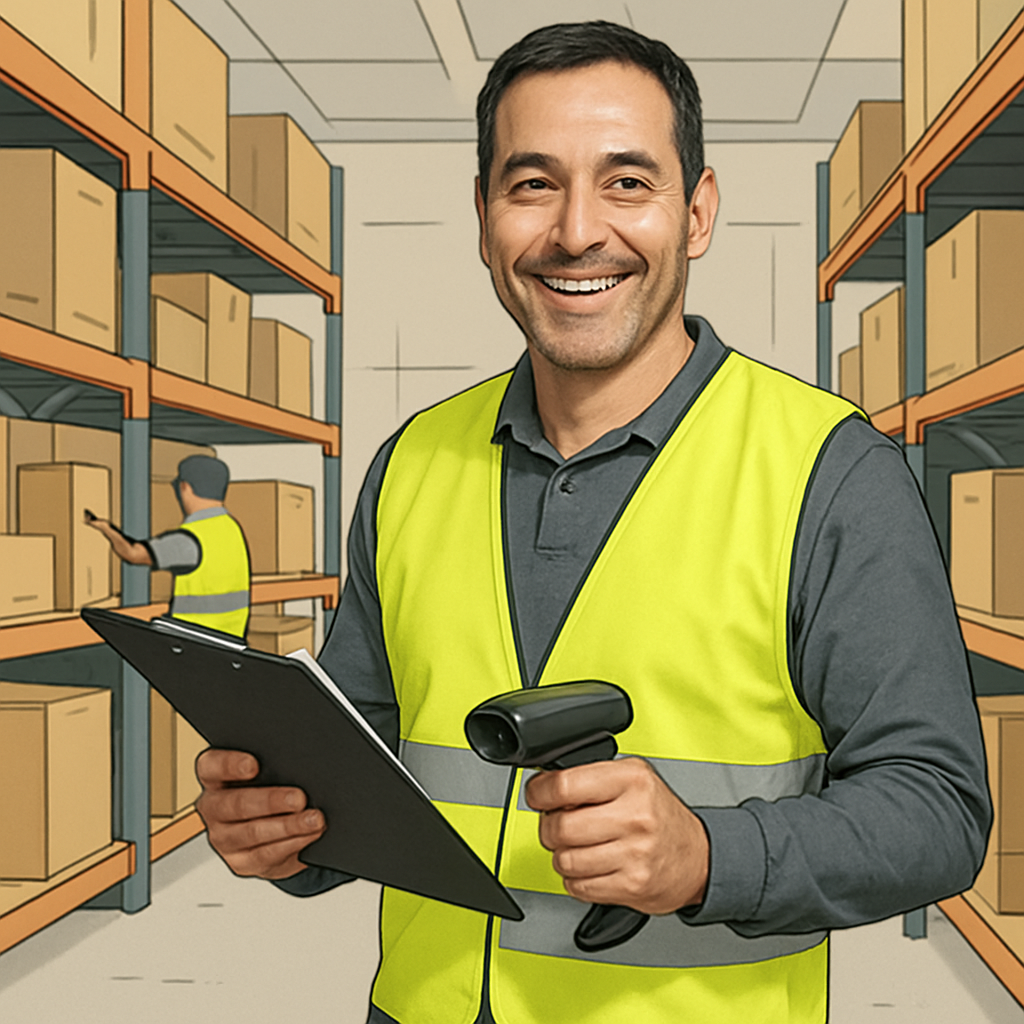
Important Considerations
To ensure error-free and compliant execution, review these key points before starting:
- Double-check sensitive or restricted zones for compliance with safety and security rules.
- Protect all customer and order data in accordance with company policies.
- Ensure real-time updates do not introduce confusion—use clear communication protocols.
- Always verify that routes account for any ongoing maintenance or blocked areas to prevent delays.
- Document any deviations for later process review and improvement.
Minutes Saved
Every Time Used
Minutes To Set Up
Workflow Guide For
Optimize Warehouse Order Picking Routes
Setting Up for Success
Before diving into the steps, gather the core resources and prepare your environment to ensure a smooth workflow implementation.
- Access to current warehouse order management/pick list system
- Accurate, up-to-date warehouse layout/map (digital or paper)
- Communication devices for staff (mobile apps, radios, printouts)
- Trained staff familiar with basic warehouse protocols
- List of any urgent, priority, or restricted orders for the day
- Process for collecting real-time updates on warehouse conditions
Important Considerations
To ensure error-free and compliant execution, review these key points before starting:
- Double-check sensitive or restricted zones for compliance with safety and security rules.
- Protect all customer and order data in accordance with company policies.
- Ensure real-time updates do not introduce confusion—use clear communication protocols.
- Always verify that routes account for any ongoing maintenance or blocked areas to prevent delays.
- Document any deviations for later process review and improvement.
Follow these steps to streamline your workflow and enhance operational efficiency in your role.
Start Here
Step 1: Gather Order Pick List Data
Prompt: "Please list all current orders to be picked today, including item SKUs, locations, and quantities, in a table format."
Goal
Collect a comprehensive list of all order items and their storage locations within the warehouse to serve as the basis for route planning.
Example
"Order 101: SKU 12345, Location: Aisle 3, Bin 6, Qty: 2. Order 102: SKU 78910, Location: Aisle 1, Bin 2, Qty: 1."
Variations
- "Provide the pick list as a downloadable CSV file."
- "Summarize today's urgent order pick items by location only."
- "Show yesterday's pick data to compare with today's."
Troubleshooting
- Missing order information: Double-check source systems or consult the warehouse management software to ensure all new orders are included.
- Incorrect item locations: Cross-verify questionable item locations against recent inventory updates.
Step 2
Step 2: Map Warehouse Layout & Identify Key Zones
Prompt: "Describe or upload the warehouse layout, labeling aisles, sections, and storage zones relevant for picking routes."
Goal
Define the physical layout and key areas of the warehouse that the picking routes will traverse, clarifying boundaries and high-traffic zones for optimal planning.
Example
"Our warehouse layout: 6 aisles (A-F), each split into bins 1–20; cold storage is Zone H, receiving is Zone R. High-traffic packing area is near Aisle A."
Variations
- "List only the aisles containing SKUs on today's pick list."
- "Highlight restricted access areas that should be avoided during routing."
- "Summarize which aisles are currently blocked or under maintenance."
Troubleshooting
- Unclear or outdated layouts: Request the latest warehouse map from facilities management.
- Not accounting for temporary obstacles: Confirm with on-shift staff about changes or obstructions before planning.
Step 3
Step 3: Generate Optimal Picking Route Suggestions
Prompt: "Based on the pick list and warehouse layout, suggest the most efficient order picking route to minimize travel time and backtracking."
Goal
Create a detailed, step-by-step picking path that allows warehouse staff to retrieve all required items in the shortest possible time with minimal walking or unnecessary repetition.
Example
"Start at Aisle 1, Bin 2 to pick Order 102, proceed through Aisle 3, Bin 6 for Order 101, then head to Zone H for refrigerated items, finishing at the packing area."
Variations
- "Generate separate picking routes for each picker/staff member."
- "Optimize the route for heavy and bulky items to be picked last."
- "Provide a visual route map or list with estimated travel time."
Troubleshooting
- Route overlaps or inefficiency: Adjust the pick sequence to avoid doubling back; try alternative route strategies if bottlenecks are detected.
- Unassigned or unclear item locations: Flag unclear items for supervisor review or substitute with next available SKU/bin.
Step 4
Step 4: Review and Adjust Routes Based on Constraints
Prompt: "Check if recommended pick routes need adjusting due to picker availability, priority orders, or real-time warehouse conditions (blocked aisles, equipment breakdown)."
Goal
Ensure the suggested routes are realistic and effective by accounting for staff schedules, urgent orders, and current warehouse conditions.
Example
"Route A reassigned to Picker #3 who starts later due to shift overlap; expedited order 104 re-routed for immediate pickup; Aisle B bypassed due to forklift blockage."
Variations
- "Re-balance routes if one picker has a heavier workload."
- "Incorporate urgent same-day orders into routes on the fly."
- "Swap out pickers and adjust route accordingly if staff call in sick."
Troubleshooting
- Last-minute staff changes: Use dynamic assignment or have backup staff trained for each route.
- Route delay due to breakdowns: Quickly reroute affected picks and notify the packing area of delays.
Step 5
Step 5: Communicate Final Routes to Picking Staff
Prompt: "Summarize finalized picking routes in a clear, actionable format for each staff member and specify how updates are communicated (e.g., printouts, mobile devices, radios)."
Goal
Ensure every picker receives their route, understands their assignments, and knows how to access updates if changes emerge during execution.
Example
"Picker 1: Route details—Aisle 1 → Aisle 3 → Zone H; receive updates via warehouse mobile app notifications."
Variations
- "Send route lists by SMS to each picker."
- "Provide route maps as printed handouts at shift start."
- "Share real-time updates over the warehouse intercom/floor radios."
Troubleshooting
- Pickers unclear about routes: Schedule a quick briefing before shift or create a FAQ for common route instructions.
- Missed updates: Ensure multiple communication channels and confirm staff receipt of route information.
Step 6
Step 7
What You'll Achieve
By following this optimized order picking workflow, you’ll create an efficient, adaptable process that minimizes travel time and errors while maximizing picker productivity. Your pickers will spend less time searching for items and more time fulfilling orders, resulting in on-time shipments and a noticeable drop in mis-picks or staff confusion. The process also supports rapid response to priority orders and day-of changes, ensuring your warehouse stays agile. Ultimately, you’ll experience satisfied staff, happy customers, and a smooth-running operation that’s ready for growth.
Measuring Your Success
Success in warehouse order picking is marked by greater speed, higher accuracy, and better coordination between staff and systems. Track your progress using these metrics:
- Order picking time per batch
- Error rate (mis-picks, missed items)
- Number of route adjustments required mid-shift
- Picker productivity (orders picked per hour)
- On-time shipment rate for picked orders
- Staff satisfaction or reduced complaints
Troubleshooting Your Workflow
Navigating workflow challenges can be daunting. This guide offers practical troubleshooting tips and innovative strategies to enhance your AI implementation.
Pro Tips & Tricks
- Batch orders by similar locations to further cut walking time.
- Use color-coded or digital route maps for clearer instructions.
- Review yesterday’s route problems for continuous improvement.
- Rotate picker assignments to avoid familiarity bias and missed items.
- Encourage staff to report blocked aisles immediately via group chat.
- Print backup pick lists in case of mobile device failure.
- Set up quick briefings at shift change to clear confusion.
- Automate data imports from order system to pick list wherever possible.
Common Issues & Solutions
Even optimized workflows can hit snags. Here are frequent problems and how to solve them:
- Issue: Missed or delayed picks due to incomplete order data.
Solution: Set automated reminders to refresh pick lists and check for late-added orders every hour. - Issue: Routes blocked by temporary obstacles.
Solution: Have staff report and broadcast updates instantly; reroute on-the-fly and use signage to alert others. - Issue: Pickers confused by route updates.
Solution: Use multi-channel communication (app + printout + radio), and recap at shift briefing. - Issue: New staff overlook restricted areas.
Solution: Highlight and review restricted zones in onboarding and route maps. - Issue: Mis-picks due to unclear location labeling.
Solution: Standardize shelf/bin labeling and provide visual references on pick lists.
Best Practices to Follow
- Regularly audit the warehouse layout and update digital maps.
- Train all staff on new routing tools and protocols before rollout.
- Enforce strict access rules for sensitive or restricted zones.
- Continuously monitor picking accuracy with spot checks.
- Document changes to routes and note reasons for future process improvement.
- Maintain clear backup communication methods for emergency updates.
- Foster knowledge sharing about trouble spots or recurring obstacles.
Stay Ahead with More Workflow Guides!
Streamline your warehouse and other operations with step-by-step workflow guides. Sign up to get proven checklists, actionable tips, and industry insights delivered to your inbox. Join our newsletter and keep your processes sharp!
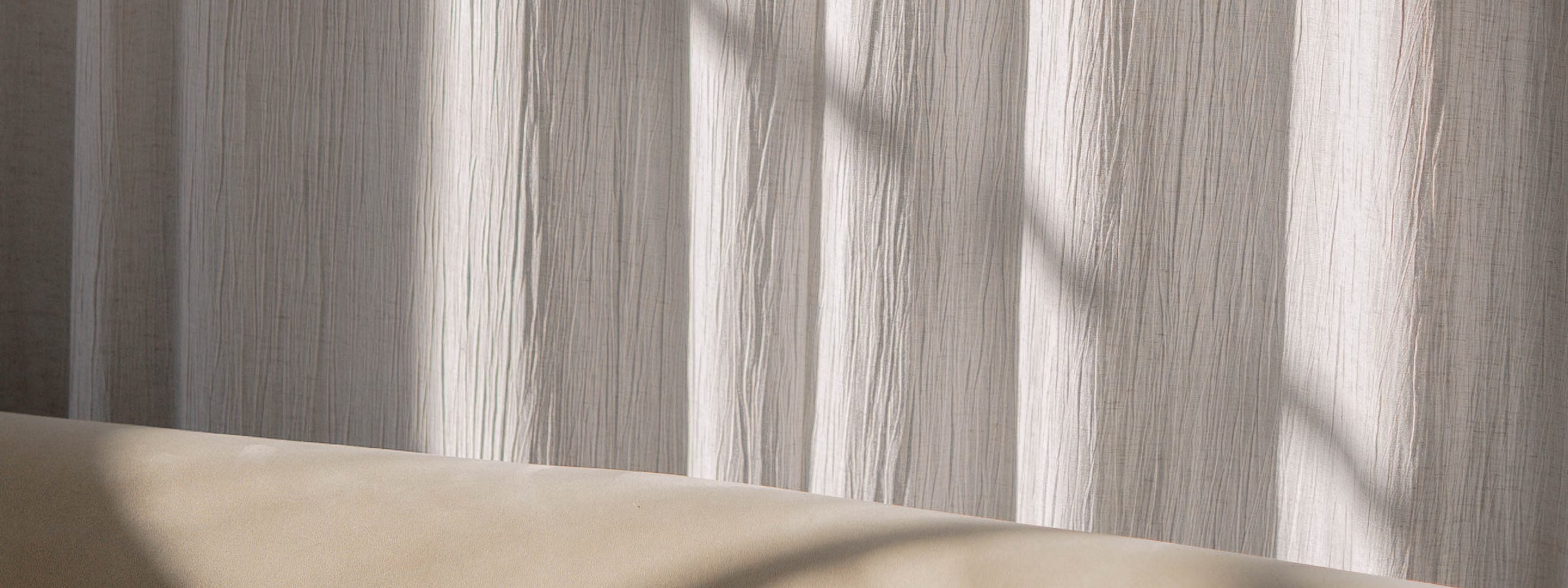
Streamline Your Daily Tasks
Discover AI solutions tailored for your role.
Multi-Modal Shipment Coordination Task
Simplify multi-modal shipments! Follow clear steps to organize, quote, and track carrier deliveries for seamless logistics. Save time now!
AI-Based Related Maintenance Suggestions
Streamline vehicle maintenance recommendations. Follow these clear steps to boost accuracy and customer trust while saving time.
Find Sheet Music & Exercises by Level & Goals
Discover how to efficiently find and assign tailored sheet music for your students. Streamline music selection with organized, actionable steps.
Stuck on a Tricky Implementation?
Let's Debug Together!
Book a 30-minute strategy session with our AI workflow wizards. We'll dive into your specific challenges, troubleshoot like pros, and map out optimization opportunities that'll make your workflows purr like a well-maintained server. No sales pitch, just solutions (and maybe a nerdy joke or two).
Explore More Guides to Enhance Your AI Implementation Journey
Discover Additional Resources Tailored for Your Industry Needs
These guides offer valuable insights and practical steps for effective AI integration.
Unlock the Potential of AI in Your Business Operations
Gain access to expert strategies and tools to streamline your processes.
Enhance Your Skills with Our Comprehensive AI Resource Guides
Find the right guide to elevate your understanding and application of AI.