Improve Ordering Accuracy via Spec Cross-Check
Struggling with flooring takeoffs means risking inaccurate orders, blown budgets, and frustrating project delays. Common issues like scattered measurements, missing product specs, or calculation errors can lead to wasted materials and unhappy clients. If flooring material takeoffs feel overwhelming or error-prone, you’re not alone—many project coordinators face the same challenges. This guide breaks down the proven, step-by-step workflow to ensure your material calculations and orders are precise, clear, and fully aligned with both project needs and supplier requirements. By following these instructions, you’ll confidently eliminate common pitfalls, save significant time, and help your projects run more smoothly from the start.
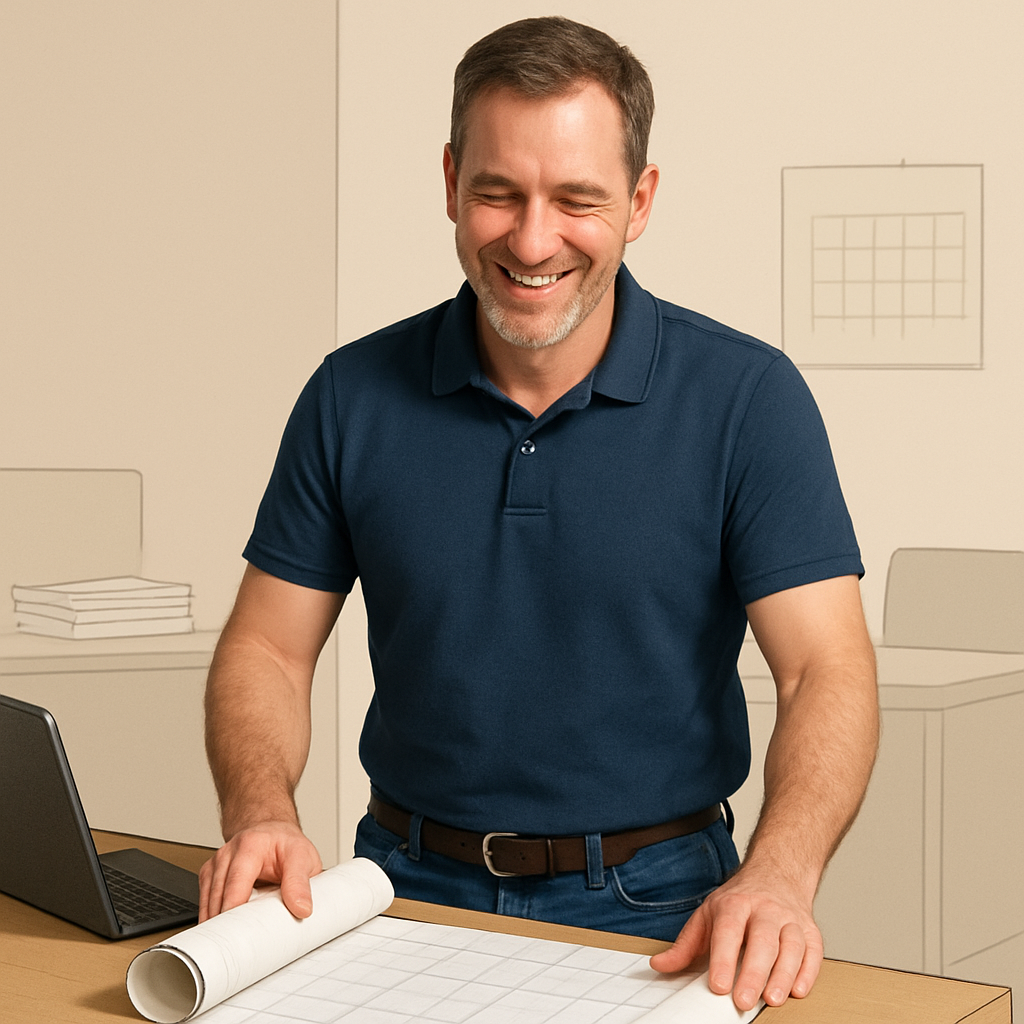
Important Considerations
Pay attention to these must-know points throughout the process to avoid costly errors or compliance problems.
- Always confirm the latest measurement data and product specs before calculations.
- Double-check for consistent units (feet vs. meters, boxes vs. pallets).
- Use only supplier-approved order forms/templates.
- Obtain explicit approval from project leads before submitting any order.
- Protect sensitive client or building data—store files securely.
- Document any changes or decisions made during project reviews.
Minutes Saved
Every Time Used
Minutes To Set Up
Workflow Guide For
Improve Ordering Accuracy via Spec Cross-Check
Setting Up for Success
Preparation is key for a smooth and reliable takeoff process. Gather the following before you begin:
- Latest floor plans or site measurement sheets
- Access to product specification data (digital or printed)
- Calculator or spreadsheet template for calculations
- Supplier order sheet template (or access to their online portal)
- Contact information for suppliers and project lead
- Notebook or digital note tool for tracking questions and follow-ups
Important Considerations
Pay attention to these must-know points throughout the process to avoid costly errors or compliance problems.
- Always confirm the latest measurement data and product specs before calculations.
- Double-check for consistent units (feet vs. meters, boxes vs. pallets).
- Use only supplier-approved order forms/templates.
- Obtain explicit approval from project leads before submitting any order.
- Protect sensitive client or building data—store files securely.
- Document any changes or decisions made during project reviews.
Follow these steps to streamline your workflow and enhance operational efficiency in your role.
Start Here
Step 1: Gather and Organize Measurement Data
"Please help me compile and organize all floor measurement data for the current project, ensuring room-by-room details are clear and accurate."
Goal
Collect all relevant floor measurements (length, width, area per room), double-checking for missing or unclear areas, so the material calculation will be based on reliable data.
Example
"Here are my measurements for Project Smith Residence: Living Room - 22'x18', Kitchen - 12'x14', Hallway - 5'x20'. Can you help organize and flag any incomplete or unusual entries?"
Variations
- "Can you list all measurements by floor level?"
- "Summarize total square footage for each room."
Troubleshooting
- Missing room data: Revisit site plans or contact the estimator for clarification.
- Inconsistent measurement units: Ask the AI to standardize all measurements (e.g., feet, meters).
Step 2
Step 2: Retrieve and Review Product Specifications
"Provide the full product specifications for the selected flooring material, including required waste factor, plank/tile size, and compatibility notes."
Goal
Confirm all relevant details about the flooring product(s), such as pack sizes, waste allowance, compatibility with existing subfloors, and installation requirements.
Example
"We plan to use Maple Plank (SKU 3399X): Each box covers 22 sq ft, planks are 6"x48", recommended 10% waste factor. Is there anything else I need to check?"
Variations
- "What is the manufacturer’s recommended waste factor for this product?"
- "List box size, coverage per box, and any trim or underlayment requirements."
- "Are there installation constraints for this flooring?"
Troubleshooting
- Missing specification sheets: Request product data from supplier or search the manufacturer’s website.
- Unclear waste calculation: Ask for industry-standard allowances if project-specific guidance isn't available.
Step 3
Step 3: Cross-Reference Measurements with Specifications
"Using the room measurements and product specs provided, calculate precise quantities needed (including waste), and highlight any discrepancies or areas for adjustment."
Goal
Accurately calculate the amount of flooring to order for each room, factoring in manufacturer guidelines, required waste factor, and specific product packaging.
Example
"Given: 800 sq ft measured, product covers 22 sq ft per box, 10% waste required. Can you show exact boxes to order and flag any measurement-product mismatches?"
Variations
- "Cross-check that all room areas match the product’s installation requirements."
- "Validate my calculation: 800 sq ft x 1.10 = 880 sq ft / 22 = 40 boxes."
Troubleshooting
- Mismatch between total area and coverage: Double-check both source data and product specs for entry errors.
- Calculation errors/missing waste: Recalculate with the correct waste factor, or ask the AI for the step-by-step formula.
Step 4
Step 4: Prepare and Review the Material Order Sheet
"Draft a detailed material order sheet based on calculated needs, listing SKUs, descriptions, quantities, and any special instructions or considerations."
Goal
Create a clear, complete order sheet that references measured needs and aligns exactly with supplier ordering formats, reducing the chance of errors or delays.
Example
"Order Sheet: Maple Plank (SKU 3399X), 40 boxes, includes 10% waste, deliver to 101 Main St. Special instructions: Confirm color batch."
Variations
- "Include a column for alternate products in case of back order."
- "Add delivery dates and project phases."
Troubleshooting
- Supplier form mismatch: Use supplier templates or request a sample order document.
- Missing fields (SKU, quantities): Double-check all line items against the finalized measurement/calculation sheet.
Step 5
Step 5: Validate and Finalize Order with Stakeholders
"Summarize the proposed order and review with project lead/supplier for approval before submission. Highlight any decisions, alternate options, or risks."
Goal
Ensure order accuracy and approval by presenting results to project stakeholders, incorporating any feedback before placing the order with suppliers.
Example
"Here’s the draft order for Project Smith: 40 boxes Maple Plank (includes waste), confirm SKU, color, and delivery schedule. Any concerns or changes before I send to supplier?"
Variations
- "Schedule a supplier call to confirm availability and lead times."
- "Send summary order as PDF for team’s sign-off."
- "Highlight backorder risk or substitutions."
Troubleshooting
- Unclear approval process: Ask the project lead/supervisor for confirmation.
- Last-minute changes: Document and implement immediately, confirming with all parties before final order placement.
Step 6
Step 7
What You'll Achieve
After successfully following this workflow, you’ll have a detailed, error-checked material order sheet ready for supplier submission—including clear measurements, correct product details, properly calculated waste, and stakeholder approvals. This outcome minimizes the risk of over- or under-ordering, ensures compliance with project and supplier requirements, and results in smoother project execution, satisfied clients, and stress-free procurement.
Measuring Your Success
Success is achieved when your flooring takeoff process produces accurate, review-ready material orders with zero rework or surprises. To track your improvement, monitor these key metrics:
- Fewer order revisions required (target: 0)
- Material waste percentage within 2% of recommended factor
- Project schedule adherence (on-time orders)
- Reduction in time spent per takeoff/project
- Zero missed or incomplete measurement data
- Consistent approval from project leads/suppliers
- Reduction in order-related callbacks or clarifications
Troubleshooting Your Workflow
Navigating workflow challenges can be daunting. This guide offers practical troubleshooting tips and innovative strategies to enhance your AI implementation.
Pro Tips & Tricks
- Standardize your data entry format for faster copy-pasting and fewer errors.
- Set up formulas in your spreadsheet to automatically include the waste factor.
- Use color-coding to easily spot flagged rooms or incomplete measurements.
- Save template “order sheets” for different product types as a baseline.
- Keep supplier contacts handy for fast resolution of missing specs.
- Batch similar projects and process takeoffs together to build efficiency.
- Automatically back up your data to avoid loss due to tech glitches.
- Review completed orders with a checklist before stakeholder review.
Common Issues & Solutions
Even with clear steps, common problems can arise. Here’s how to spot and resolve them quickly:
- Issue: Incomplete or unclear room measurements.
Solution: Go back to floor plans, site surveys, or request clarification from the measuring team. - Issue: Product specification data missing or outdated.
Solution: Contact supplier or search manufacturer website for current spec sheets. - Issue: Misapplied waste factor results in over/under-ordering.
Solution: Always use the manufacturer’s recommended waste allowance and verify the calculation in your spreadsheet. - Issue: Order form rejected by supplier due to formatting or missing info.
Solution: Use current supplier templates and run a checklist before submission. - Issue: Last-minute product substitutions.
Solution: Document changes, recalculate needs, and communicate immediately with all stakeholders.
Best Practices to Follow
- Always review measurements and specs against original source documents before calculating.
- Include at least one round of independent cross-checks for critical data.
- Document all material calculations and order decisions for auditability.
- Consistently apply manufacturer’s waste factor—never guess.
- Stay up to date with supplier requirements and update templates accordingly.
- Utilize digital tools for measurement storage and calculations, reducing manual errors.
- Clarify any uncertainties with stakeholders before order submission.
- Regularly review and update your workflow for continuous improvement.
Ready to Take Your Project Accuracy Up a Notch?
Sign up for our newsletter to get more workflow guides, productivity tips, and industry solutions delivered straight to your inbox.
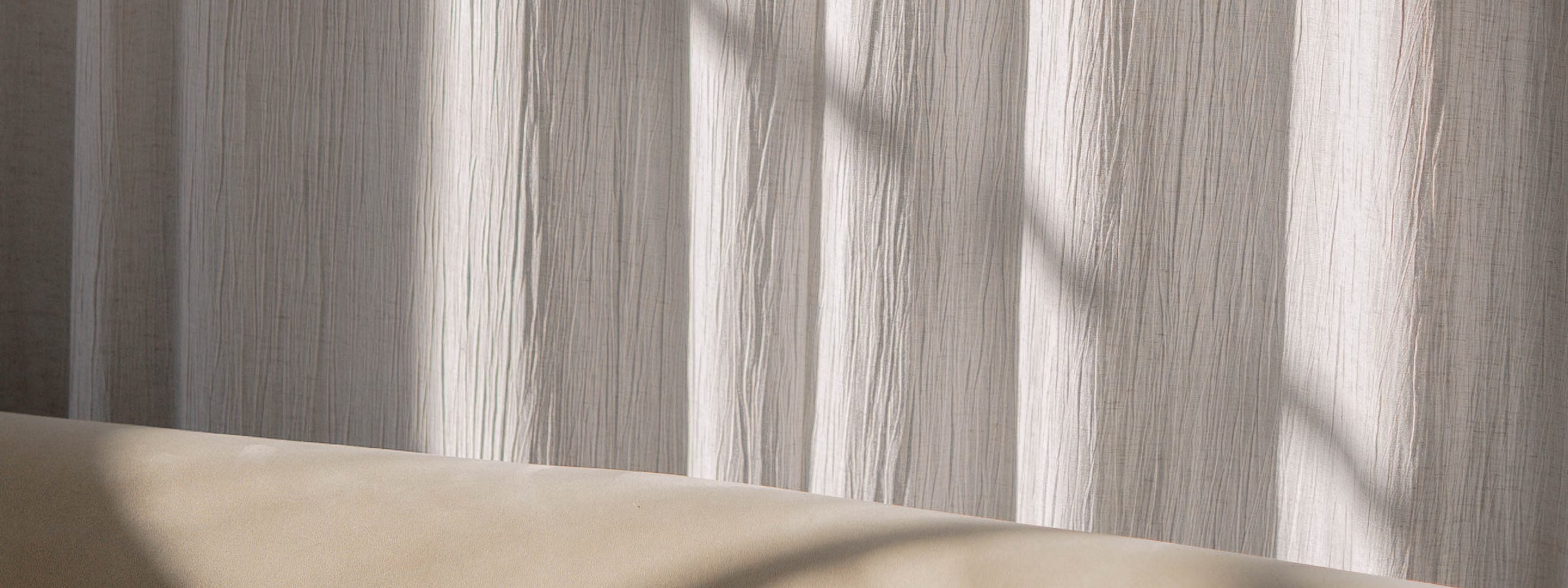
Streamline Your Daily Tasks
Discover AI solutions tailored for your role.
Multi-Modal Shipment Coordination Task
Simplify multi-modal shipments! Follow clear steps to organize, quote, and track carrier deliveries for seamless logistics. Save time now!
AI-Based Related Maintenance Suggestions
Streamline vehicle maintenance recommendations. Follow these clear steps to boost accuracy and customer trust while saving time.
Find Sheet Music & Exercises by Level & Goals
Discover how to efficiently find and assign tailored sheet music for your students. Streamline music selection with organized, actionable steps.
Stuck on a Tricky Implementation?
Let's Debug Together!
Book a 30-minute strategy session with our AI workflow wizards. We'll dive into your specific challenges, troubleshoot like pros, and map out optimization opportunities that'll make your workflows purr like a well-maintained server. No sales pitch, just solutions (and maybe a nerdy joke or two).
Explore More Guides to Enhance Your AI Implementation Journey
Discover Additional Resources Tailored for Your Industry Needs
These guides offer valuable insights and practical steps for effective AI integration.
Unlock the Potential of AI in Your Business Operations
Gain access to expert strategies and tools to streamline your processes.
Enhance Your Skills with Our Comprehensive AI Resource Guides
Find the right guide to elevate your understanding and application of AI.