Auto Generate POs at Reorder Points
Are you tired of surprise stockouts, urgent customer delays, or the chaos of last-minute order scrambles? Managing parts inventory efficiently is a constant challenge for service and repair businesses, especially when every minute lost equals both revenue and reputation at stake. The good news: you don’t need to fly blind or rely on outdated workarounds. This step-by-step guide walks you through a proven workflow for reviewing current inventory, confirming supplier details, generating and editing purchase orders, and ensuring timely reorders. By adopting this process, you’ll minimize errors, reduce manual labor, and create the peace of mind that comes with smooth, reliable inventory management.
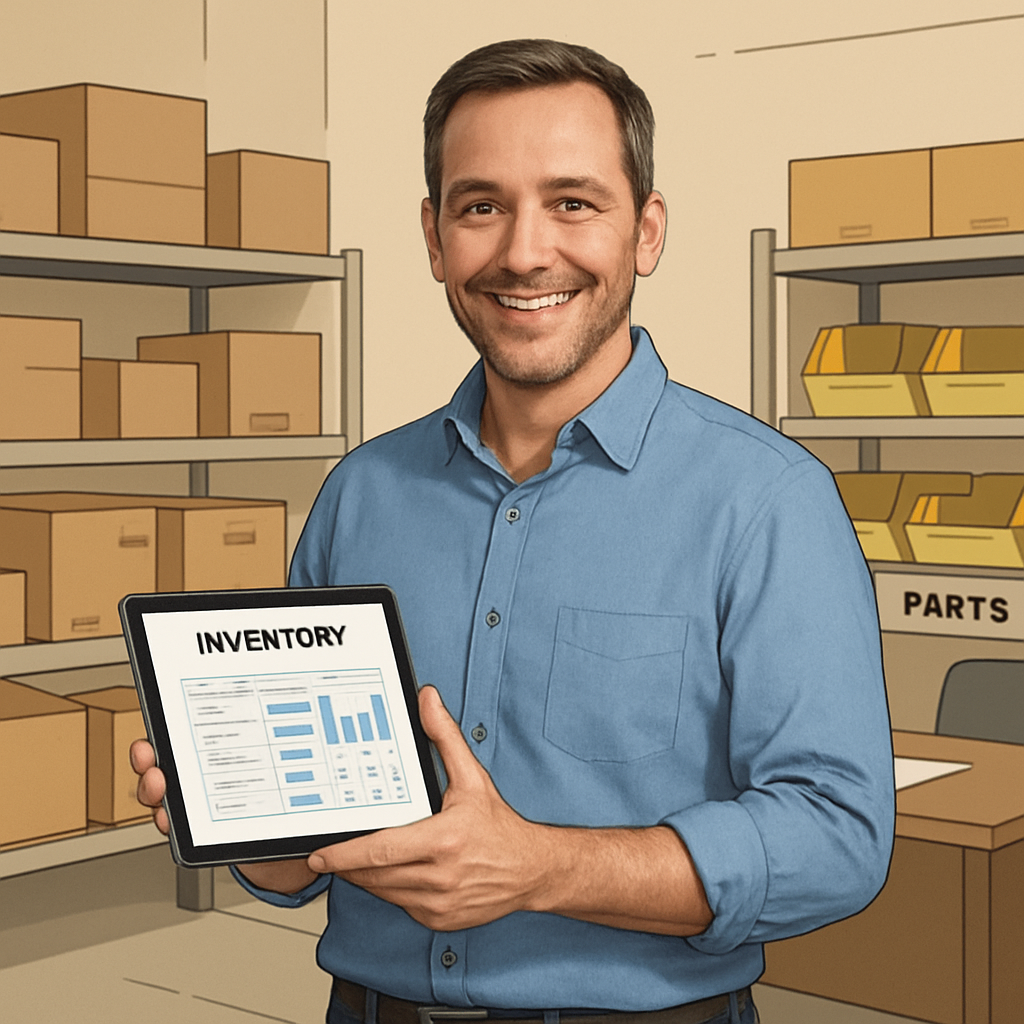
Important Considerations
Before executing this workflow, ensure compliance and accuracy to avoid costly missteps.
- Double-check item reorder points for accuracy—incorrect thresholds cause either overstock or shortages.
- Always validate supplier information prior to order—outdated contacts lead to missed orders.
- Protect sensitive supplier terms and pricing when sharing documentation.
- Monitor for duplicate items or suppliers to prevent redundant orders.
- Observe any industry-specific compliance for electronic orders or procurement records.
Minutes Saved
Every Time Used
Minutes To Set Up
Workflow Guide For
Auto Generate POs at Reorder Points
Setting Up for Success
Gather these essentials to start the workflow smoothly and avoid disruptions during the process:
- Access to a current inventory management system
- List of predefined reorder points for all stocked parts
- Updated supplier directory with contacts and ordering methods
- Permissions to generate and edit purchase orders
- Latest product and past order reports
Important Considerations
Before executing this workflow, ensure compliance and accuracy to avoid costly missteps.
- Double-check item reorder points for accuracy—incorrect thresholds cause either overstock or shortages.
- Always validate supplier information prior to order—outdated contacts lead to missed orders.
- Protect sensitive supplier terms and pricing when sharing documentation.
- Monitor for duplicate items or suppliers to prevent redundant orders.
- Observe any industry-specific compliance for electronic orders or procurement records.
Follow these steps to streamline your workflow and enhance operational efficiency in your role.
Start Here
Step 1: Review Current Inventory Levels and Reorder Points
"Show me a summary of my current parts inventory with each item's stock level and its corresponding reorder point."
Goal
To quickly get an accurate overview of parts that are at or below their predefined reorder points, ensuring no critical stockouts occur.
Example
"Display all parts with quantities at or below reorder thresholds in the brake components category."
Variations
- "List all parts where current stock <= reorder point."
- "Which items in my inventory are close to hitting their reorder point?"
- "Show out-of-stock parts and their last order dates."
Troubleshooting
- Inventory data appears outdated: Ensure your inventory management system is synced and up to date before running the check.
- Some parts missing from list: Double-check that reorder points are correctly set for all inventory items.
Step 2
Step 2: Confirm and Update Supplier Details
"Provide the latest supplier information for the items at or below reorder points, including contact and preferred ordering method."
Goal
To ensure purchase orders will be sent to the correct, current supplier and avoid delays due to outdated contacts or ordering errors.
Example
"Update the supplier record for 'Bosch brake pads' to use the new email address bosch-parts2024@distributor.com."
Variations
- "Which suppliers handle these low-stock items?"
- "Edit the purchasing contact info for supplier XYZ."
- "Add a new preferred supplier for AC compressors."
Troubleshooting
- Unable to locate supplier: Verify the item is linked to a supplier in your system.
- Supplier info incorrect: Cross-check with most recent invoices or supplier communications.
Step 3
Step 3: Generate Draft Purchase Orders for Review
"Create draft purchase orders for all items at or below their reorder points, grouped by supplier. Provide a summary preview."
Goal
To automatically prepare purchase orders covering all necessary items, minimizing manual entry and clerical errors.
Example
"Generate a draft PO for all items in the engine parts category that are below reorder points for my review."
Variations
- "Prepare draft POs for review by supplier."
- "Show me draft orders only for imported items."
Troubleshooting
- Items missing from draft PO: Check item settings and ensure reorder points and suppliers are correctly associated.
- Duplicate items on multiple POs: Confirm that items are not listed with multiple suppliers or have duplicate entries.
Step 4
Step 4: Review, Edit, and Approve Purchase Orders
"Show me the draft POs. Let me edit quantities and approve or reject each order with comments if needed."
Goal
To ensure accuracy and completeness before purchase orders are finalized and sent to suppliers, catching any errors or necessary adjustments.
Example
"Change the order quantity for 'Shell Rotella T6 Oil' from 36 to 48 units, and add a note: 'Increase stock for upcoming service promotion.'"
Variations
- "Edit PO details for review before sending."
- "Reject PO for wiper blades, add comment: using surplus stock."
- "Approve all POs except those over $500 for special review."
Troubleshooting
- PO editing not saving: Check user permissions and make sure your changes are properly saved/synced.
- Order quantity fields uneditable: Ensure draft status is active, not already approved/finalized.
Step 5
Step 5: Finalize and Submit Purchase Orders to Suppliers
"Send all approved purchase orders to their respective suppliers using the preferred method (e.g., email, EDI)."
Goal
To transmit accurate purchase orders to suppliers promptly, starting the replenishment process and minimizing potential delays.
Example
"Email the approved PO for 'Continental tires' to continental-dealer@partsupplier.com with a summary attached."
Variations
- "Send all approved POs via EDI where available, email the rest."
- "Only send urgent POs immediately; save routine ones for batch processing."
Troubleshooting
- PO not sent notification: Check system send queue or email logs for errors and retry if necessary.
- Supplier did not receive PO: Confirm correct supplier contact info and request confirmation receipt.
Step 6
Step 7
What You'll Achieve
By the end of this workflow, you will have generated, reviewed, and submitted accurate purchase orders for all needed parts, ensuring your stock levels are healthy and replenished on time. This means you’ll see fewer urgent “out of stock” scenarios, decreased downtime, and satisfied internal or external customers. You'll gain greater oversight and confidence in your supply chain, while freeing up time to focus on more strategic or profitable activities. Ultimately, you’ll establish a reputation for reliability and responsiveness—foundations for business growth and customer trust.
Measuring Your Success
Track the impact of your new workflow with these key indicators to ensure your inventory management is running at peak efficiency.
- Reduction in parts stockouts per month
- Decrease in emergency/rush purchase orders
- Percent of orders submitted with zero errors
- Time spent per reorder cycle
- Supplier response and on-time fulfillment rate
Troubleshooting Your Workflow
Navigating workflow challenges can be daunting. This guide offers practical troubleshooting tips and innovative strategies to enhance your AI implementation.
Pro Tips & Tricks
- Set calendar reminders for routine inventory checks to stay ahead of reorders.
- Tag fast-moving or mission-critical parts for prioritized review and alerts.
- Use batch editing features to update multiple reorder points or supplier contacts quickly.
- Archive old suppliers to avoid confusion in selection menus.
- Customize PO templates to auto-populate standard fields for speed.
- Leverage reporting tools to spot usage patterns and refine future reorder points.
- Keep an emergency order process documented for true “fire drill” situations.
Common Issues & Solutions
Anticipate these roadblocks, and resolve them proactively with these troubleshooting tips.
- Issue: Inventory data is missing or outdated.
Solution: Sync your system with recent receipts and usage before running reports. - Issue: PO not saving or approval changes are lost.
Solution: Ensure you have correct permissions and are in the current draft session. - Issue: Duplicate suppliers or items on POs.
Solution: Clean up old supplier/item records and confirm associations before order creation. - Issue: Supplier does not receive the purchase order.
Solution: Verify email addresses and request confirmations for all submissions. - Issue: Order is rejected due to pricing or terms.
Solution: Review latest supplier agreements ahead of time and note special cases in comments.
Best Practices to Follow
- Review inventory levels and reorder points monthly—even for slow-moving items.
- Validate supplier contact/terms at least quarterly or after significant changes.
- Implement approval checkpoints for all POs above a set dollar value.
- Maintain clear audit trails for every order placed.
- Regularly train team members on the workflow and system updates.
- Consolidate orders by supplier to leverage shipping efficiencies.
- Monitor fill rates and address chronic supply chain delays proactively.
Stay Ahead in Inventory Management
Want practical guides, time-saving checklists, and expert inventory tips in your inbox? Subscribe to our WorkflowGuide.com newsletter for the latest updates and resources to keep your business running smoothly!
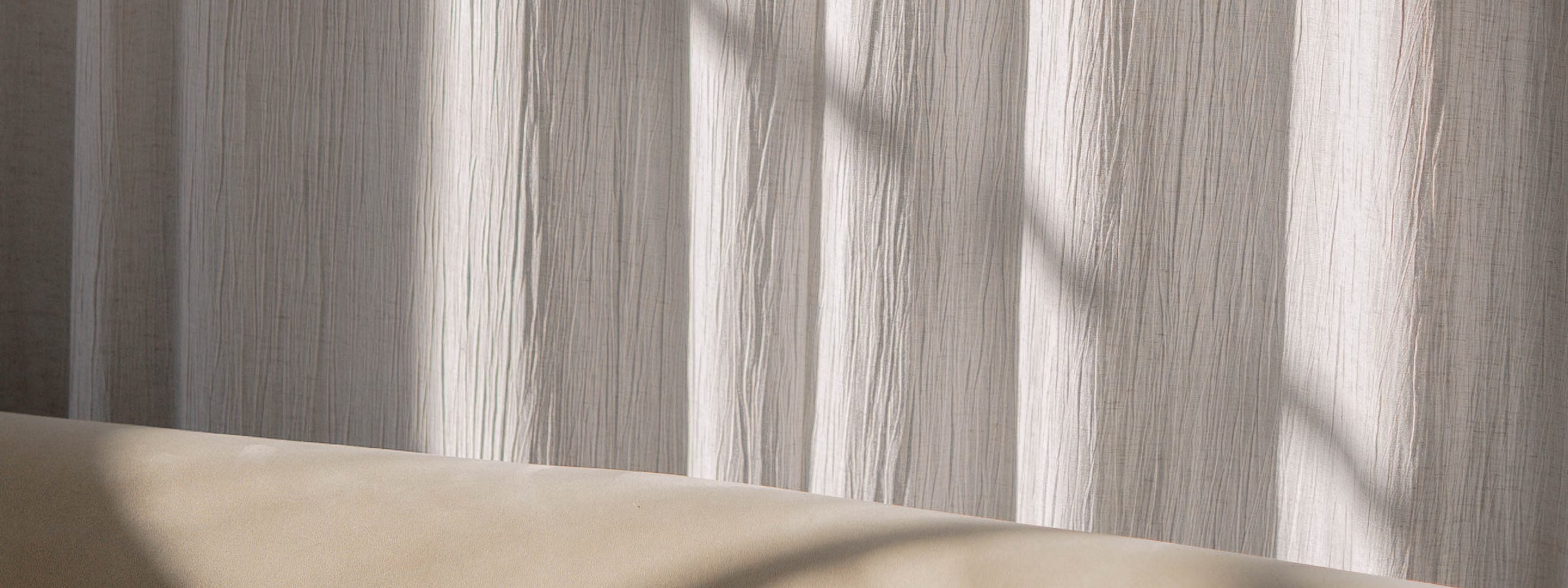
Streamline Your Daily Tasks
Discover AI solutions tailored for your role.
Multi-Modal Shipment Coordination Task
Simplify multi-modal shipments! Follow clear steps to organize, quote, and track carrier deliveries for seamless logistics. Save time now!
AI-Based Related Maintenance Suggestions
Streamline vehicle maintenance recommendations. Follow these clear steps to boost accuracy and customer trust while saving time.
Find Sheet Music & Exercises by Level & Goals
Discover how to efficiently find and assign tailored sheet music for your students. Streamline music selection with organized, actionable steps.
Stuck on a Tricky Implementation?
Let's Debug Together!
Book a 30-minute strategy session with our AI workflow wizards. We'll dive into your specific challenges, troubleshoot like pros, and map out optimization opportunities that'll make your workflows purr like a well-maintained server. No sales pitch, just solutions (and maybe a nerdy joke or two).
Explore More Guides to Enhance Your AI Implementation Journey
Discover Additional Resources Tailored for Your Industry Needs
These guides offer valuable insights and practical steps for effective AI integration.
Unlock the Potential of AI in Your Business Operations
Gain access to expert strategies and tools to streamline your processes.
Enhance Your Skills with Our Comprehensive AI Resource Guides
Find the right guide to elevate your understanding and application of AI.